The aviation industry is a major contributor to carbon emissions, but the trend is shifting towards greener alternatives. A remarkable breakthrough could be on the horizon with the advent of aviation electrification. Yet, current technology only permits small electric aircraft, with their electric motors generating mere hundreds of kilowatts of power. Achieving this shift for larger, heavier aircraft, such as commercial airliners, requires a significant upgrade – megawatt-scale motors driven by hybrid or turbo-electric propulsion systems.
Answering this call for innovation, an impressive team of engineers from the Massachusetts Institute of Technology (MIT) is spearheading the creation of a 1-megawatt motor. This leap forward in technology could prove instrumental in moving towards electrifying larger aircraft. The MIT team has successfully designed and tested the critical components of the motor. Their detailed computations affirm that these interconnected parts can work synergistically to generate one megawatt of power, maintaining a size and weight that aligns with current small aero-engines.
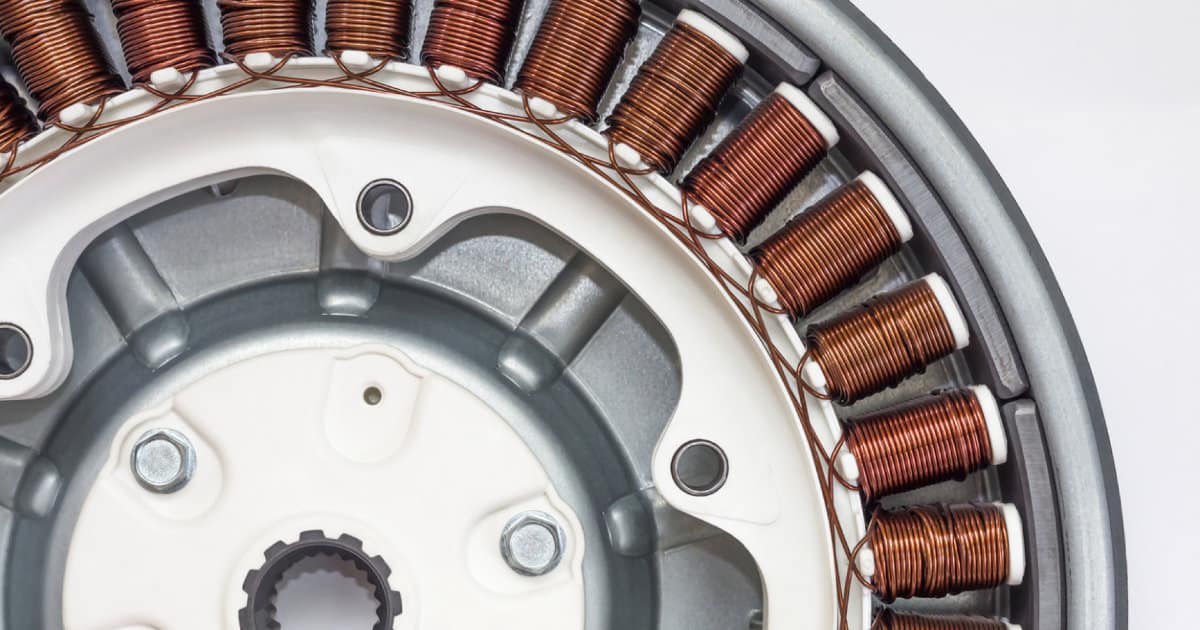
When it comes to entirely electric applications, the MIT engineers envision the 1-megawatt motor working in tandem with a power source such as a battery or a fuel cell. This combination would convert electrical energy into mechanical work, providing the power required for a plane’s propellers. Additionally, this advanced electrical machine could be paired with a conventional turbofan jet engine, forming a hybrid propulsion system. This setup would offer electric propulsion during certain flight stages.
Zoltan Spakovszky, the T. Wilson Professor in Aeronautics and the Director of the Gas Turbine Laboratory (GTL) at MIT, leads this groundbreaking project. According to him, “Regardless of the energy carrier used—be it batteries, hydrogen, ammonia, or sustainable aviation fuel—megawatt-class motors will be instrumental in making aviation greener.”
The team, consisting of faculty, students, and research staff from the GTL and the MIT Laboratory for Electromagnetic and Electronic Systems, plans to present their innovative work at a special session of the American Institute of Aeronautics and Astronautics – Electric Aircraft Technologies Symposium (EATS). The project is sponsored by Mitsubishi Heavy Industries (MHI).
Environmental scientists have underscored the importance of global carbon dioxide emissions reaching net-zero by 2050 to avert severe climate change repercussions. Achieving this target for aviation requires massive strides in designing unconventional aircraft, advanced materials, smart fuel systems, and efficient electrified propulsion, says Spakovszky. Numerous aerospace companies are focused on creating megawatt-scale electric machines capable of powering passenger aircraft while remaining lightweight.
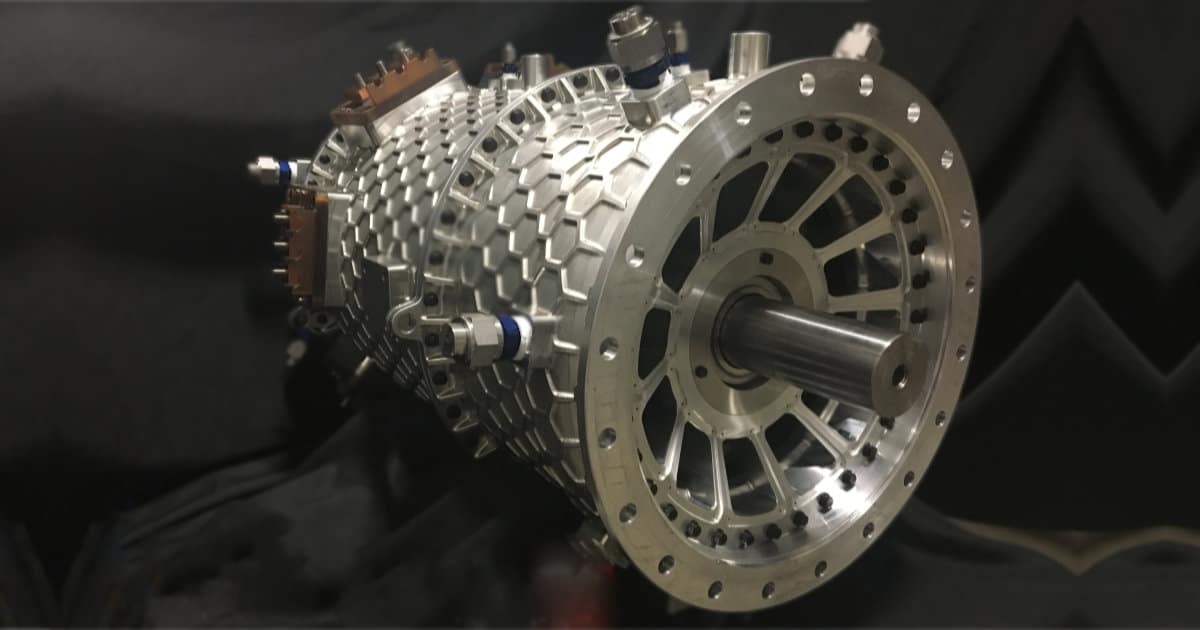
Electric motors have been in existence for over 150 years, and the idea has always been simple: larger appliances or vehicles require larger copper coils and magnetic rotors, making the machine heavier. However, weight is a critical factor for airplanes, and the team had to design a powerful yet compact and lightweight architecture.
The resultant motor design and its accompanying power electronics are each roughly the size of a suitcase and weigh less than an adult passenger. The motor’s primary components include a high-speed rotor, a compact low-loss stator, an advanced heat exchanger, and a distributed power electronics system. This co-optimized integrated design allows the motor to reach the required specific power at one megawatt.
The team’s pioneering approach combines conventional and cutting-edge methods for electric machine development. Their work is promising, offering robustness and efficiency that could meet future aircraft’s practical needs. Once the motor’s design is proven effective as a whole, it could power regional aircraft or function alongside conventional jet engines in hybrid-electric propulsion systems. In the future, the design’s principles could be scaled up to multi-megawatt motors, enabling larger passenger planes’ electrification.
As Spakovszky optimistically puts it, “We are on a good trajectory.” This path may well lead to an aviation industry that is not only more efficient but also more environmentally friendly. In his words, “addressing the 2050 climate grand challenge is of utmost importance; working with electrical engineering faculty, staff, and students for this goal can draw on MIT’s breadth of technologies so the whole is greater than the sum of the parts.”
Frequently Asked Questions About Electric Aircraft
Electric aircraft hold considerable potential in reducing aviation’s carbon footprint. Traditional jet fuel is a significant source of carbon emissions. By contrast, electric aircraft utilize energy from cleaner sources, such as batteries or fuel cells. By replacing or supplementing conventional engines with electric motors, these aircraft can significantly reduce or even eliminate emissions during flight. The shift to electric aviation also promotes the broader use of renewable energy in electricity generation, further contributing to global carbon reduction efforts.
Despite their potential, several challenges exist in developing electric aircraft. One of the key challenges is energy density. Current battery technology does not provide the same amount of energy per unit weight as jet fuel, making it challenging to power larger commercial aircraft over long distances. Heat management is another significant issue because electric motors generate heat that must be effectively dissipated to prevent damage. Additionally, integrating electric propulsion systems into existing aircraft designs poses considerable engineering challenges. Despite these obstacles, continuous advancements in technology and engineering are progressively overcoming these hurdles.
Source
Massachusetts Institute of Technology: Website